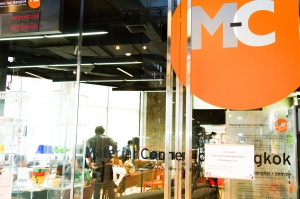
ตามติดโครงการ The Corporation 2 โดยห้องสมุด Material Connexion ตอนที่ 5 “ทำความเข้าใจและทดลองวัสดุ”
เรื่อง : วิสาข์ สอตระกูล
คู่ที่หนึ่ง : นวัตกรรมไบโอเซลลูโลส VS แฟชั่นแนวทดลอง ผู้ผลิตวัสดุ : สมบัติ รุ่งศิลป์ (บจก.ไทยนาโนเซลลูโลส) ผู้ผลิตวัสดุไบโอเซลูโลสแบบแห้ง
นักออกแบบ : กฤษณ์ เย็นสุดใจ โจทย์ความเป็นไปได้ในการออกแบบ : ผลิตภัณฑ์ในกลุ่มไลฟ์สไตล์ ความงาม และของตกแต่ง |
เซลลูโลสแบบแห้ง “กลายพันธุ์” ได้
ฝ่ายนักออกแบบ กฤษณ์ เย็นสุดใจ เริ่มต้นอธิบายถึงผลลัพธ์จากการทดลองเลี้ยงไบโอเซลลูโลสในพื้นที่ขนาดใหญ่ (ทดลองเลี้ยงในอ่างกลมขนาดเส้นผ่าศูนย์กลางประมาณ 1.3 เมตร และใช้กระดาษเป็นฝาคลุมปิดด้านบนแทนพลาสติก) และอย่างที่กล่าวไปในตอนที่แล้วว่าเขาใช้เวลาเลี้ยงไบโอเซลลูโลสรอบนี้ประมาณ 15 วัน ซึ่งถือว่านานกว่าปกติ ซึ่งผลลัพธ์ที่ได้ก็คือตัววัตถุดิบเติบโตดีจนมีความหนาและเหนียวขึ้นกว่าแต่ก่อนมาก (ประมาณ 50 เท่าของการผลิตปกติ)
สมบัติ รุ่งศิลป์ ฝ่ายเจ้าของวัสดุเองมีความเชื่อว่า อาจเป็นเพราะอากาศสามารถซึมผ่านกระดาษเข้าไปสัมผัสกับแบคทีเรียได้อย่างสม่ำเสมอ (ต่างจากการผลิตปกติที่ใช้พลาสติกคลุมและแง้มขอบไว้) จึงทำให้เกิดปรากฏการณ์ที่เหนือความคาดหมายเช่นนี้ขึ้น
อย่างไรก็ดี เมื่อกฤษณ์นำวัตถุดิบดังกล่าวมาตากแดดทิ้งไว้ 2 สัปดาห์ เขาก็พบว่ามันได้เปลี่ยน “คุณสมบัติสำคัญ” บางอย่างไป ข้อแรกก็คือจากที่ทุกคนเคยเข้าใจว่าวัสดุไบโอเซลลูโลสนั้น “ไวต่อความชื้น” สามารถดูดซับความชื้นหรือน้ำกลับคืนได้อย่างรวดเร็ว (และจะคืนสภาพเป็นเซลลูโลสแบบเปียก) สิ่งที่เกิดขึ้นในรอบนี้กลับต่างไปอย่างสิ้นเชิง
กฤษณ์กล่าวว่าไบโอเซลลูโลสชุดนี้เหมือนจะ “กลายพันธุ์” ไปแล้ว คือเมื่อโดนน้ำก็ไม่ยอมคืนสภาพ ไม่สามารถรีบให้เรียบดังเดิมได้ แถมมีความเหนียวสุดๆ จนกรรไกรแทบตัดไม่เข้า และที่สำคัญคือวัสดุชุดนี้ไม่ยอมดูดความชื้นกลับเข้าไปเต็มๆ เหมือนแต่ก่อน หยดน้ำจะกลิ้งอยู่แค่ที่พื้นผิวด้านบนและทำให้วัสดุมีความชื้นเพิ่มขึ้นนิดหน่อยเท่านั้น
“กินได้” คือสุดยอดของความบริสุทธ์
จากคุณสมบัติใหม่ที่เกิดขึ้นข้างต้น กฤษณ์มองว่าไบโอเซลลูโลสแบบแห้งนี้น่าจะนำไปต่อยอดเป็นผลิตภัณฑ์พวก “กระเป๋าถือ” หรือ “แอคเซสซอรี่” ได้สบายๆ เพราะมีทั้งผิวสัมผัส (Texture) และความแข็งคงทน (ขึ้นรูปได้) ซึ่งถือว่าใกล้เคียงกับวัสดุ “หนัง” อย่างมาก
จากนั้นเมื่อเขาปรึกษากับฝ่ายผู้ผลิตวัสดุ ทั้งคู่ก็เห็นตรงกันว่าอยากจะพัฒนาผลิตภัณฑ์ตัวใหม่นี้ให้มีความ “บริสุทธ์และเป็นธรรมชาติ” อย่างสูงสุด ยกตัวอย่างเช่นถ้าสามารถกินได้เลยก็จะดีมาก กฤษณ์ค้นคว้าลงลึกต่อไปว่าในตลาดตอนนี้มี สี หมึกพิมพ์ กระดาษ หรือองค์ประกอบอื่นใดอีกบ้างที่บริสุทธ์เพียงพอถึงขั้น “กินได้” เพราะเขาคิดจะนำองค์ประกอบเหล่านี้มาผนวกเข้ากับการออกแบบผลิตภัณฑ์ให้มากที่สุด
นอกจากนั้น กฤษณ์ยังได้บูรณการไอเดีย “บริสุทธ์-กินได้” เข้ากับวัสดุไบโอเซลูโลสแบบโพลีเมอร์ด้วย โดยเขาคิดว่าแผ่นเจลโพลีเมอร์แบบเปียกนี้ ถ้าใส่สีผสมอาหารลงไปและนำไปขึ้นรูปใน mold ลักษณะต่างๆ ก็อาจต่อยอดไปเป็นผลิตภัณฑ์ในกลุ่ม Health & Beauty ได้อีกมาก
คู่ที่สอง : ปุยนุ่นธรรมชาติ VS งานออกแบบไลฟ์สไตล์โปรดักท์
ผู้ผลิตวัสดุ : วิญญู วรัญญู (หจก. ที่นอนจารุภัณฑ์) ผู้ผลิตนุ่นธรรมชาติ
นักออกแบบ : จุฑามาส บูรณะเจตน์ และ ปิติ อัมระรงค์ จาก O-D-A (Object Design Alliance)
โจทย์ความเป็นไปได้ในการออกแบบ : สินค้าเฟอร์นิเจอร์ที่บอกเล่าเรื่องราวและคุณสมบัติพิเศษของนุ่น
3 วิธี “แบ่งห้อง” ให้นุ่น
จุฑามาส บูรณะเจตน์ นักออกแบบสาวจาก O-D-A กล่าวว่า เธอและคู่หู ปิติ อัมระรงค์ ได้ศึกษาลงลึกถึงกระบวนการผลิตสินค้าจากวัสดุนุ่น โดยโจทย์ที่ตั้งไว้ในขั้นแรกก็คือ การค้นหาวิธีที่จะใช้งานวัสดุนุ่นด้วย “เทคนิค” ที่ต่างออกไป
ในที่สุด ทั้งสองก็พบว่าการทำงานกับนุ่นนั้นจำเป็นต้องมีการ “แบ่งช่อง” เพื่อใช้งานเสมอ เช่น ถ้าจะยัดนุ่นทำที่นอน ผู้ผลิตก็ต้องเย็บช่องเล็กๆ เป็นโมดูลไว้ภายในเฟรมของที่นอนเสียก่อน จากนั้นจึงค่อยใส่นุ่นลงไปให้เต็มพื้นที่ช่องเหล่านี้ เพราะนี่คือกรรมวิธีเดียวที่จะรักษา “ฟอร์ม” ของตัวที่นอนเอาไว้ได้ (มิฉะนั้นนุ่นก็จะหนีและไหลไปเรื่อยๆ ทำให้ที่นอนยุบตรงนั้น พองตรงนี้ ไม่คงสภาพอย่างที่ควรจะเป็น)
จุฑามาสและปิติได้นำแนวคิดนี้ไปศึกษาต่อ และทดลองสร้างรูปแบบ “การแบ่งห้องให้นุ่น” ขึ้นเป็น 3 ลักษณะ คือ
1. แบ่งเป็นโมดูล - ถือเป็นเทคนิคดั้งเดิม แต่อาจปรับเปลี่ยนฟอร์มของช่องให้แปลกใหม่ขึ้นได้
2. แบ่งเป็นเลเยอร์ - แยกห้องเป็นชั้นๆ แต่ละชั้นมีลักษณะซ้อนทับกัน
3. แบ่งเป็นหน่วยอิสระ - โดยแต่ละหน่วยมีความเป็นอิสระ แยกจากกันโดยเด็ดขาด
4 กลุ่มสินค้าที่นำมาทดลองเทคนิค
1. ที่นอนเด็ก - ทดลองออกแบบผลิตภัณฑ์ด้วยเทคนิคการแบ่งห้องแบบเลเยอร์ เพื่อให้สามารถแยกชั้นไปทำความสะอาดได้ง่าย
2. เตียงนอนผู้ใหญ่ - ใช้เทคนิคดั้งเดิมของการแบ่งห้องแบบโมดูลที่เชื่อมต่อถึงกัน แต่ได้ลองออกแบบตัวที่นอนให้ผสานเป็นชุดเดียวกับเตียงนอน (Bed frame) ด้วย ซึ่งจะทำให้เตียงชุดนี้มีลักษณะพับเก็บได้ ง่ายต่อการขนส่ง / โยกย้าย รวมทั้งมีดีไซน์ที่ดูทันสมัยและไฮเอนด์มากยิ่งขึ้น
3. Bean bag - นำเทคนิคการแบ่งช่องเป็นหน่วยๆ แบบแยกอิสระมาประยุกต์ใช้ โดยพวกเขาได้ลองทำไส้ในของ bean bag ให้เป็นก้อนผ้ากลมๆ ยัดด้วยนุ่น ซึ่งแตกต่างจาก Bean bag ที่เห็นทั่วไปในท้องตลาด
4. ที่นั่งแพทเทิร์น - คาดว่าจะผสมผสานเทคนิคการแบ่งช่องหลายๆ แบบ และอาจลองใช้เทคนิคการแบ่งช่องแบบหลอดเพื่อช่วยในเรื่องโครงสร้างด้วย
คู่ที่สาม : ไม้อัดปิดผิว VS ดีไซน์เพื่อคุณภาพชีวิต
ผู้ผลิตวัสดุ : บจก.ลีโอวูด อินเตอร์เทรด ผู้ผลิตวัสดุไม้แปรรูปและไม้เอ็นจีเนียร์
นักออกแบบ : นิพิฐพนธ์ ภูริชบุญทรัพย์ จาก Millennium Ducks Design Store
โจทย์ความเป็นไปได้ในการออกแบบ : พัฒนาลวดลายและรูปแบบของวัสดุเพื่อให้ง่ายต่อการใช้งานที่หลากหลาย
นิพิฐพนธ์ ภูริชบุญทรัพย์ นักออกแบบจาก Millennium Ducks Design Store ได้ย้ำถึงเป้าหมายในการพัฒนาผลิตภัณฑ์ครั้งนี้ว่า เขาต้องการจะสร้าง “วัตถุดิบใหม่” เพื่อทดแทนสิ่งที่มีอยู่เดิมในท้องตลาด และจะต้องทำวัตถุดิบนี้ให้มีคุณสมบัติที่ดีกว่าเดิมในแง่การใช้งาน รวมทั้งตอบโจทย์ด้านสิ่งแวดล้อม และมีศักยภาพเชิงพาณิชย์ในระดับสูงด้วย (ต้องทำขายตลาดแมสให้ได้)
ด้วยกรอบความคิดดังกล่าวนี้ นิพิฐพนธ์จึงได้เข้าไปศึกษา “เศษขยะอุตสาหกรรม” ของโรงงานลีโอวูด ซึ่งมีทั้งเศษไม้เอ็มดีเอฟ เศษไม้วีเนียร์ เศษขี้เลื่อยจากไม้ยางพารา ไม้ยูคาลิปตัส ไม้โอ๊ค ไม้แอช ฯลฯ ที่เหลือทิ้งอยู่เป็นจำนวนมาก ต่อจากนั้นเขาได้คัดเลือกเทคนิคการผลิตบางอย่างที่น่าสนใจจากภายในโรงงาน อาทิเช่น การอัดและรีดแผ่นไม้วีเนียร์ การเย็บขอบแผ่นผิวไม้ การซ่อมแซมสีและตำหนิบนผิวไม้ ฯลฯ โดยตั้งใจว่าจะนำเทคนิคพวกนี้มาลองทำงานกับเศษวัสดุในขั้นตอนต่อไป
แนวทางการพัฒนา “วัสดุเอาท์ดอร์” ตัวใหม่
วิธีที่หนึ่ง : นิพิฐพนธ์ลองนำเศษไม้วีเนียร์ส่วนที่ถูกตัดทิ้ง (ส่วนหัวและท้ายของแผ่น) มาเย็บรวมเข้าด้วยกันหลายๆ ชิ้นแบบเกยทับกันไปมา (ภายใต้เฟรมขนาด 120 x 240 ซม.) โดยแผ่นแรกนั้นเขาจะวางเศษไม้ในแนวนอน ส่วนแผ่นที่สองวางในแนวตั้ง (ขวางเกรนไม้สลับกัน) ทำแต่ละชั้นสลับกันไปแบบนี้จนได้ประมาณ 8-9 ชั้น จากนั้นในขั้นต่อไปก็ให้ประกบติดกันด้วยกาว อัดรีดจนเป็นแผ่น (pressure) และไสผิวให้เรียบอีกครั้งเพื่อให้ได้ความหนา 20 มม.
นิพิฐพนธ์คาดว่ากระบวนนี้จะทำให้เกิดเอฟเฟกต์ใหม่ๆ บนชั้นผิวหน้าของวัสดุ ซึ่งจะดูมีความเป็นศิลปะแบบคาดเดาไม่ได้ นอกจากนั้น ในกระบวนการผลิตจริงลูกค้าน่าจะสั่งผลิตแบบคละสีคละลายได้ตามต้องการ (ตามแต่ประเภทเศษวัสดุที่เลือกมาใช้) ซึ่งผลลัพธ์ก็จะมีความเป็นไปได้ที่หลากหลายมาก
วิธีที่สอง : ทำงานกับเศษไม้วีเนียร์ที่เหลือทิ้งเช่นเดิม แต่เปลี่ยนวิธีการจัดเรียงเกรนไม้ใหม่ โดยในวิธีที่สองนี้นิพิฐพนธ์จะเรียงเกรนไม้ทุกแผ่นในแนวเดียวกันหมด (ไม่ขวางเสี้ยน) จากนั้นก็นำไม้แต่ละแผ่นมาเชื่อมต่อกันเป็นแนวยาว และม้วนเก็บด้วยเครื่องจักรจนเกิดเป็น “ทรงกระบอก” คล้ายต้นซุง (ตรงนี้ถือเป็นกระบวนการแปรรูปไม้แบบย้อนกลับ คือ จากเศษไม้ - ติดกาวต่อเข้าด้วยกัน - รีดเป็นแผ่น - ม้วนเป็นทรงกระบอก)
โดยในขั้นสุดท้ายนิพิฐพนธ์คิดว่าเขาจะลองนำต้นซุงที่เกิดขึ้นใหม่นี้ไปผ่าเป็นแว่นๆ อีกครั้งตามแนวยาว หรืออาจจะผ่าแนวอื่นก็ได้แล้วแต่เอฟเฟกต์ที่ลูกค้าต้องการ ทั้งนี้ผลลัพธ์ที่ได้น่าจะออกมาดูแปลกตา มีลวดลายที่ผิดไปจากธรรมชาติ และให้อารมณ์สนุกสนานได้กว่าปกติ
วิธีที่สาม : แนวทางนี้นิพิฐพนธ์ตั้งใจจะนำเศษไม้และเศษขี้เลื่อยมาผลิตเป็นเอ็มดีเอฟที่แข็งแรงขึ้น เหนียวขึ้น และดัดได้ โดยหลักการก็คือ เขาจะนำเศษไม้และเศษวัสดุอุตสาหกรรมมาผสมรวมกันและรีดให้เป็นแผ่น จากนั้นก็นำมาซ้อนทับกันเป็นชั้นๆ โดยในระหว่างชั้นนี้จะต้องมีโครงสร้างบางอย่างช่วยยึดโยงอยู่ภายใน
ในชั้นแรกอาจเริ่มจากการวางเศษไม้ในแนวนอนก่อน จากนั้นค่อยผสม “เศษขี้เลื่อย” ลงไปพร้อมกับกาวชนิดพิเศษ (ชนิดเอาท์ดอร์) ส่วนในชั้นที่สองเขาจะใส่เศษวัสดุอุตสาหกรรมที่มีความเป็น “เส้นใยชิ้นยาวๆ” ขัดสลับลงไป (ใช้หลักการขัดกันของเส้นใยเป็นตัวช่วย) ท้ายที่สุดนิพิฐพนธ์มองว่า วัสดุตัวนี้น่าจะเหมือนกับการมีโครงสร้างของ “เหล็กเส้น” ที่เข้าไปแทรกตัวอยู่ภายในเนื้อมวลของวัสดุบางอย่าง
เขาจินตนาการว่าผลลัพธ์ของแนวทางนี้น่าจะทำให้เอ็มดีเอฟตัวใหม่มีความแข็งแรงและเหนียวขึ้นอย่างมาก ไม่แน่อาจจะสามารถผลิตชิ้นงานที่มีความยาวได้ถึง 4 เมตรก็ได้
ท้ายสุดนิพิฐพนธ์เชื่อว่าวัตถุดิบใหม่ที่อาจเกิดขึ้นจากทั้งสามแนวทางนี้น่าจะสามารถพัฒนาสำหรับใช้งานแบบเอาท์ดอร์ (หรือกึ่งเอาท์ดอร์) ได้ทั้งหมด เพราะปัจจัยหลักของการทำวัสดุเอาท์ดอร์นั้นน่าจะอยู่ที่ “กาว” และ “เทคนิคการผลิต” ที่เข้ามาเกี่ยวข้องมากกว่า โดยเขาคาดคะเนว่าความสามารถในการใช้งานแบบเอาท์ดอร์จะขึ้นอยู่กับกาว 70% และอยู่ที่วัสดุตั้งต้น 30%
คู่ที่สี่ : ผ้าผสมเส้นใยธรรมชาติ VS งานศิลปะเท็กซ์ไทล์
ผู้ผลิตวัสดุ : บัณฑิต พงศาโรจนวิทย์ (บริษัท ไทยนำโชคเท็กซ์ไทล์ จำกัด) ผู้ผลิตวัสดุผ้าผสมเส้นใยธรรมชาติ
นักออกแบบ : ขนิษฐา นวลตรณี
โจทย์ความเป็นไปได้ในการออกแบบ : นำวัสดุเส้นใยธรรมชาติไปประยุกต์ใช้ในแอพลิเคชั่นอื่นๆ
ต่อยอดสิ่งทอไทยด้วยเส้นใย “ต้มยำ”
นักออกแบบ ขนิษฐา นวลตรณี รับหน้าที่อธิบายความก้าวหน้าของโครงการแทนฝ่ายเจ้าของวัสดุอีกครั้ง โดยเธอกล่าวว่านอกจากเส้นใยสับปะรดที่ทางเจ้าของวัสดุได้พัฒนาก้าวไกลไปมากแล้ว เธอยังมีความสนใจที่จะนำ “เส้นใยข่า” และ “เส้นใยตะไคร้” (ที่เจ้าของวัสดุเรียกว่า “เส้นใยต้มยำ”) มาทดลองพัฒนาด้วย เพราะเส้นใยทั้งสองชนิดนี้ถือเป็นวัตถุดิบท้องถิ่นไทยแท้ มีความแปลกใหม่สำหรับตลาดนานาชาติ และน่าจะมีศักยภาพมากพอในการต่อยอดทั้งในเชิงพาณิชย์ การผลิต และการสร้างเรื่องราวให้กับแบรนด์
ขนิษฐาเล่าว่าเส้นใยทั้งสามชนิดที่เธอเลือกทำงานด้วยในครั้งนี้ (ใยสับปะรด ใยข่า ใยตะไคร้) ทางโรงงานไทยนำโชคได้ทดลองปั่นเป็นด้ายออกมาบ้างแล้ว โดยสามารถทำขึ้นในสองวิธี คือ
1) ปั่นแบบอุตสาหกรรม ซึ่งจะออกมาเป็นเส้นด้ายกลมปกติ แต่มีข้อแม้ว่าต้องผสมเส้นใยฝ้ายลงไปด้วยเป็นส่วนใหญ่ (เพราะเครื่องจักรหลักเป็นเครื่องจักรปั่นฝ้าย)
2) ปั่นแบบกาลาโบ้ มีความพิเศษคือจะทำให้ผลผลิตที่ได้มีลักษณะคล้ายการปั่นด้วยมือ เส้นด้ายจะมีขนาดเล็กใหญ่สลับกันไป โดยวิธีนี้เราสามารถผสมฝ้ายหรือวัสดุอื่นๆ เข้าไปได้ตลอด ดังนั้นถ้าอยากผสมเส้นใยที่มีสีสลับสับเปลี่ยนกันไป หรืออยากให้เนื้อผ้ามี texture ที่ไม่เท่ากันตลอดทั้งผืน การปั่นแบบกาลาโบ้นี้ก็สามารถทำได้หมด
อย่างไรก็ดี ขนิษฐาเผยว่าด้วยข้อจำกัดเรื่องเทคโนโลยีการปั่นเส้นใยของโรงงาน (ที่ไม่สามารถปั่นแบบ wet-spinning ได้) เธอคาดว่าผลิตภัณฑ์สุดท้ายที่จะเกิดขึ้นในโครงการนี้อาจไม่เหมาะกับการทำเสื้อผ้าเครื่องนุ่งห่ม แต่น่าจะเหมาะกับการเป็นผ้าทำกระเป๋าหรือไว้ใช้ในอุตสาหกรรมเฟอร์นิเจอร์มากกว่า
เพราะ “ธรรมชาติคืออนาคต”
แนวคิดการทำธุรกิจของคุณบัณฑิต พงศาโรจนวิทย์ ที่ว่า “Nature is Future” ได้กลายเป็นแรงบันดาลใจให้ขนิษฐาอยากพัฒนาสิ่งทอให้ก้าวไปในทิศทางนี้ให้มากที่สุด โดยเธอตั้งใจจะดึงคุณลักษณะเด่นของเส้นใยต่างๆ ขึ้นมาให้คนเห็น และอาจมีการผสมเปลือกของเส้นใยเข้าไปบ้าง เพื่อดึงภาพลักษณ์ความเป็นธรรมชาติออกมาให้ชัดเจนด้วย
นอกจากนั้น ด้วยความที่สิ่งทอของโรงงานไทยนำโชคฯ ดูมีความเป็น “แฮนด์คราฟท์” นิดๆ (ทั้งๆ ที่ความจริงผลิตแบบอุตสาหกรรม) ขนิษฐาเองก็คิดว่าทางโรงงานน่าจะมีโอกาสพัฒนาผลิตภัณฑ์ตัวใหม่ๆ เพื่อเจาะตลาดญี่ปุ่นได้ เพราะผู้บริโภคในตลาดนี้มักจะมีรสนิยมที่ชื่นชอบอะไรที่ดูคราฟท์อยู่แล้ว
ในแง่ของแนวคิดการออกแบบ ขนิษฐามองว่าเทคนิคการทอปัจจุบันที่โรงงานไทยนำโชคฯ ทำได้ เช่นการทอผสมสีแบบแรนดอม (Random) หรือการใช้เส้นด้ายหลายขนาดเพื่อสร้างผิวสัมผัส (Texture) ล้วนมีความสอดคล้องกับการชูภาพลักษณ์เรื่องความเป็นธรรมชาติอยู่แล้ว เธอจึงถือว่าเรื่อง “ทักษะ” กับ “แนวคิด” นั้นได้เดินมาลงตัวกันพอดี และไม่มีอะไรน่าหนักใจในจุดนี้
ถึงขณะนี้ขนิษฐาได้สรุปโจทย์ให้กับตัวเองไว้ 3 ข้อ คือ
1. เธอจะออกแบบเรื่อง “ลวดลายและสีสัน” ให้สิ่งทอนี้มีความแปลกตา สร้างสรรค์ และเป็นศิลปะมากที่สุด
2. จะยังคงใช้เทคนิคการผลิตแบบอุตสาหกรรมที่ทางโรงงานคุ้นเคยดี
3. จะดึงภาพลักษณ์เรื่อง “ความเป็นธรรมชาติ” และ “ความคราฟท์” ออกมาให้ได้อย่างสูงสุด