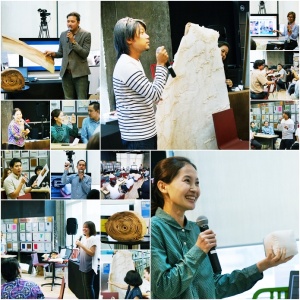
ตามติดโครงการ The Corporation 2 โดย Material Connexion ตอนที่ 6 “Sketch & Prototype”
เรื่อง : วิสาข์ สอตระกูล / สุวิทย์ วงศ์รุจิราวาณิชย์
คู่ที่หนึ่ง : นวัตกรรมไบโอเซลลูโลส VS แฟชั่นแนวทดลอง ผู้ผลิตวัสดุ : สมบัติ รุ่งศิลป์ (บจก.ไทยนาโนเซลลูโลส) ผู้ผลิตวัสดุไบโอเซลูโลสแบบแห้ง นักออกแบบ : กฤษณ์ เย็นสุดใจ โจทย์ความเป็นไปได้ในการออกแบบ : ผลิตภัณฑ์ในกลุ่มไลฟ์สไตล์ ความงาม และของตกแต่ง |
นักออกแบบ กฤษณ์ เย็นสุดใจ นำเสนอโครงร่างของการทำงานในรอบนี้อย่างสั้นๆ ด้วยการใช้ภาพประกอบเพียงไม่กี่ภาพ เขาเกริ่นนำว่าสำหรับนักออกแบบที่มีอายุเข้าสู่วัยกลางคนแล้วอย่างเขา ที่มาของแรงบันดาลใจต่างๆ มักจะเกิดจากการนึกย้อนทบทวนไปในอดีต ซึ่งคงแตกต่างจากนักออกแบบรุ่นใหม่ๆ ที่มักจะมองไปถึงสิ่งที่อยู่ข้างหน้าเสมอ
ต่อจากนั้น กฤษณ์ได้สรุปแนวทางการทำงานไว้เป็นหัวข้อหลักๆ 4 หัวข้อ คือ
1. Material Process: สรุปวิธีการเฉพาะเพื่อพัฒนาเซลลูโลสแบบแห้งไว้เป็นวัสดุตั้งต้นดังนี้
- เลี้ยงเชื้อจุลินทรีย์จากข้าวให้เกิดเป็นเส้นใยเซลลูโลสความหนาประมาณ 1 ซม. (ใช้เวลา 10 วัน)
- นำไปผ่านกระบวนการแยกเชื้อแบคทีเรีย (ไล่เชื้อ / กำจัดน้ำตาลออกจากตัวเซลลูโลสให้หมด)
- นำแผ่นเซลลูโลสที่ได้มาเรียงซ้อนกัน 10 แผ่น และอัดรวมกันด้วยวิธีรีดร้อนจนกลายเป็นแผ่นเดียว
- นำไปตากแดดจนแห้งสนิท พร้อมนำไปใช้งาน
2. Surface Design: ผิวสัมผัสจะเป็นเรื่องที่สำคัญมากสำหรับการออกแบบผลิตภัณฑ์ครั้งนี้ และตัวกฤษณ์เองก็เป็นนักออกแบบที่ให้ความสำคัญกับเรื่องวัสดุมาโดยตลอด ซึ่งเขาอยากจะให้วัสดุเซลลูโลสแบบแห้งนี้มีความเป็น “ลูกครึ่ง” ระหว่างกระดาษกับหนัง อย่างไรก็ดี เขาคิดว่ายังพอมีเวลาที่จะลองเล่นกับเทคนิคใหม่ๆ และสำรวจความเป็นไปได้เพิ่มเติมให้กับตัววัสดุอีก
3. Design Concept: ในส่วนนี้หมายถึงการขมวดแนวคิดผลิตภัณฑ์เพื่อให้คนทั่วไปเข้าใจได้ง่าย (รวมถึงรู้ด้วยว่าจะนำผลิตภัณฑ์สุดท้ายไปใช้งานอย่างไร) ซึ่งกฤษณ์ได้กำหนด keyword คร่าวๆ สำหรับการออกแบบไว้แล้ว เช่น Cross Culture, Cross Current, Imitation, Replica, Mutation, No design, Rearrange, Copy และ Handcraft
4. Product Design: นำเสนอภาพร่างเปรียบเทียบระหว่างชิ้นงานที่เป็น “แรงบันดาลใจ” จากอดีต กับชิ้นงานใหม่ที่จะผ่าน “เทคนิค” การเล่นกับตัววัสดุของเขา (ภายใต้แนวคิด 100% Leather VS 100% Bacterial Cellulose from Rice culture) ซึ่งในการนี้กฤษณ์ได้เลือกรูปทรงของ “กระเป๋าถือ” รุ่นคลาสสิกต่างๆ มาใช้เป็นต้นแบบฝั่งแรงบันดาลใจ (อันได้แก่ กระเป๋า Hermes, Chanel และ Louis Vuitton) ทั้งนี้เพื่อจะให้คนทั่วไปสามารถเข้าใจถึง Final Product ที่เขาพยายามจะนำเสนอได้ง่ายที่สุดนั่นเอง
ข้อเสนอแนะจากผู้เข้าร่วมเวิร์คชอป - ถ้าจะทำกระเป๋าจากวัสดุนี้ให้ใช้งานได้จริง มีความทนทาน คงสภาพ ฯลฯ น่าจะต้องมีการใส่สารบางอย่างเพิ่มเติม เช่น สารกันเชื้อรา สารคงความชื้น หรือมีการใช้เลเยอร์เข้าช่วยในการตัดเย็บด้วย ทั้งนี้เพื่อจะให้ตัววัสดุหยุดดูดซับความชื้นจากสภาพแวดล้อม และสร้างความคงตัว/ความถาวรได้ดียิ่งขึ้น |
คู่ที่สอง: ปุยนุ่นธรรมชาติ VS งานออกแบบไลฟ์สไตล์โปรดักท์ ผู้ผลิตวัสดุ: วิญญู วรัญญู (หจก. ที่นอนจารุภัณฑ์) ผู้ผลิตนุ่นธรรมชาติ นักออกแบบ: จุฑามาส บูรณะเจตน์ และ ปิติ อัมระรงค์ จาก O-D-A (Object Design Alliance) โจทย์ความเป็นไปได้ในการออกแบบ: สินค้าเฟอร์นิเจอร์ที่บอกเล่าเรื่องราวและคุณสมบัติพิเศษของนุ่น |
จุฑามาส บูรณะเจตน์ และ ปิติ อัมระรงค์ จาก O-D-A นำเสนอแบบร่างพร้อมต้นแบบในการพัฒนาผลิตภัณฑ์โดยได้แบ่งออกเป็น 2 แนวทาง คือ
1. เก้าอี้ Bean bag: ทีมงานได้นำแนวคิดการแบ่งนุ่นออกเป็นห้องๆ มาสร้างเอกลักษณ์ให้กับผลิตภัณฑ์ใหม่ โดยเลือกใช้วัสดุ 2 ประเภท คือ 1) วัสดุแบบทึบสำหรับใช้บริเวณรองนั่ง และ 2) วัสดุแบบโปร่ง (คล้ายตาข่าย) สำหรับโชว์ลูกบอลยัดนุ่นที่อยู่ภายใน ทั้งนี้เพื่อจะแสดงให้เห็นถึงความต่างระหว่าง Bean bag ทั่วไปที่ใช้เม็ดพลาสติก กับ Bean bag แบบใหม่ที่กำลังพัฒนานี้ ในส่วนของรูปทรง ขนาด และแพทเทิร์นการตัดเย็บ ทั้งสองเล่าว่าลูกบอลยัดนุ่นที่ใช้บรรจุภายในต้นแบบนี้ได้ผ่านการทดสอบด้านรูปทรงมาแล้ว โดยพบว่ารูปทรงสี่เหลี่ยม “ลูกเต๋า” ที่ประหยัดเนื้อที่การตัดผ้ามากที่สุด กลับขึ้นรูปได้ยากกว่าเมื่อเทียบกับรูปทรงกลมแบบ “ลูกบอล” ที่ใช้แพทเทิร์นผ้าเพียงแค่สองชิ้น (แพทเทิร์นเดียวกับลูกเบสบอล)
จากนั้นทีมงานได้ลองกำหนดขนาดที่เหมาะสมให้กับลูกบอลนุ่นนี้ พวกเขาเลือกทำลูกบอลขนาด 64 กรัม มีเส้นผ่าศูนย์กลาง 16 เซ็นติเมตร โดยผลิตออกมาทั้งสิ้น 50 ลูก เพื่อใช้ทดสอบประสิทธิภาพการนั่งในเบื้องต้น
แต่ผลปรากฏว่าจำนวนลูกบอลนุ่นที่เตรียมไว้ยังน้อยเกินไป ไม่สามารถใช้ทดสอบกับ Bean bag ต้นแบบที่ทำไว้สำหรับผู้ใหญ่ได้ ทีมงานจึงแก้ไขด้วยการปรับโครงต้นแบบให้มีขนาดเล็กลงก่อน เพราะต้องการจะทดสอบเรื่อง “ความรู้สึกในการนั่ง” ให้ได้ ซึ่งจากการลองนั่งของผู้ร่วมเวิร์คชอปหลายๆ ท่าน ก็มีคำแนะนำว่าขนาดของลูกบอล ณ จุดนี้อาจจะใหญ่เกินไป แถมมีความแข็งทำให้นั่งไม่สบายตัว ซึ่งทางคุณวิญญู (ผู้ผลิตวัสดุ) ก็อธิบายว่านุ่นจะอ่อนตัวและนุ่มลงเองหลังจากใช้งานไปแล้วระยะหนึ่ง ความแข็งนี้จะเกิดขึ้นเฉพาะการใช้งานในช่วงต้นเท่านั้น
ข้อเสนอแนะจากผู้เข้าร่วมเวิร์คชอป - ถ้าลองทำลูกบอลนุ่นขนาดเล็กเพื่อใช้ร่วมกับลูกบอลนุ่นขนาดใหญ่อาจจะช่วยให้นั่งสบายตัวมากขึ้น |
2. ที่นั่งแบบพับเชื่อมขึ้นรูป: ทีมงานได้ลองสร้างแพทเทิร์นผ้า 2 แบบที่สามารถพับหรือเชื่อมต่อเข้าหากัน และขึ้นรูปเป็น “ที่นั่งแบบมีพนักพิง” ได้ในตัว โดยในการนี้พวกเขาได้ลองยัดนุ่นเข้าไปที่ความหนาประมาณ 1 เซ็นติเมตรด้วย
2.1 ที่นั่งรูปใบไม้ ออกแบบวิธีการเย็บ การพับ และการเชื่อม ให้ชิ้นงานสามารถขึ้นรูปเป็นที่นั่งได้อย่างง่ายๆ โดยรอยเย็บที่ดูคล้ายกับลายเส้นบนใบไม้นั้นก็จะเป็น “ตัวแบ่งช่อง” สำหรับการใส่นุ่นภายใน (เพื่อกันนุ่นไหลมากองรวมกัน) และในขณะเดียวกันก็จะทำหน้าที่เป็น “รอยพับขึ้นรูป” ที่จะสร้างรูปทรงของตัวใบไม้ขึ้นมาด้วย
2.2) ที่นั่งทรงสามเหลี่ยม เกิดจากการนำแพทเทิร์นผ้ายัดนุ่น 3 ชิ้นมาล็อคติดกันในตำแหน่งที่กำหนดไว้ ซึ่งตำแหน่งดังกล่าวนี้ก็จะดัดโครงของชิ้นผ้าให้กลายเป็นรูปสามเหลี่ยมที่มีช่องสำหรับให้คนนั่งเล่นตรงกลาง ที่น่าสนใจคือแนวคิดนี้ผู้ใช้สามารถเลือกสีสันให้กับตัวผลิตภัณฑ์ได้ เช่น อาจใช้ผ้า 3 ชิ้น 3 สี หรืออาจจะเล่นเป็นสีโมโนโทนแบบ 3 เฉดก็ได้ และข้อดีอีกข้อของชิ้นงานนี้ก็คือ มันจะประหยัดเนื้อที่ในการขนส่งได้มาก ซึ่งก็เท่ากับเป็นการประหยัดการใช้พลังงานไปในตัวด้วย
ข้อเสนอแนะจากผู้เข้าร่วมเวิร์คชอป - ให้ระวังเรื่องรูปทรงที่อาจทำให้นั่งไม่สบายตัว ควรต้องศึกษาเรื่องสัดส่วนที่เหมาะสมกับร่างกายของผู้ใช้ด้วย |
คู่ที่สาม : ไม้อัดปิดผิว VS ดีไซน์เพื่อคุณภาพชีวิต ผู้ผลิตวัสดุ : บจก.ลีโอวูด อินเตอร์เทรด ผู้ผลิตวัสดุไม้แปรรูปและไม้เอ็นจีเนียร์ นักออกแบบ : นิพิฐพนธ์ ภูริชบุญทรัพย์ จาก Millennium Ducks Design Store โจทย์ความเป็นไปได้ในการออกแบบ : พัฒนาลวดลายและรูปแบบของวัสดุเพื่อให้ง่ายต่อการใช้งานที่หลากหลาย |
นิพิฐพนธ์ ภูริชบุญทรัพย์ จาก Millennium Ducks นำเสนอตัวอย่าง section ของ “ท่อนซุง” ที่เกิดจากกระบวนการย้อนรอยเศษวัสดุวีเนียร์ให้กลับไปเป็นรูปทรงกระบอกขนาดเส้นผ่าศูนย์กลางประมาณ 1 ฟุต (Reverse process) โดยในการนี้นิพิฐพนธ์เล่าว่าเขาได้ขอให้ช่างจากโรงงานลีโอวูดฯ ทดลองม้วนแผ่นไม้บางๆ ซึ่งทำขึ้นจากเศษวัสดุวีเนียร์ (หลายๆ แผ่นที่ต่อกันเข้าด้วยกาว) เข้าไปในเครื่องจักรอย่างรวดเร็วภายใน 1 วัน
ผลจากการทดลองปรากฏว่าได้ทำให้เกิดแพทเทิร์นแปลกตาขึ้นในมวลเนื้อของตัววัสดุ มีโพรงอากาศเกิดขึ้นหลายแห่ง และมี error จากการม้วนที่ไม่เหมือนกับการเกิดวงปีของไม้ตามธรรมชาติ ถือเป็นผลลัพธ์ที่ทางนิพิฐพนธ์เองก็ตื่นเต้นและพอใจเป็นอย่างมาก เขากล่าวว่า effect ที่เกิดขึ้นนี้น่าจะสร้างความเป็นไปได้ใหม่ๆ ให้กับการต่อยอดวัสดุนี้ได้อีกมาก
นิพิฐพนธ์แนะว่าข้อดีของการมี error ในมวลวัสดุ (ที่เป็นโพรงอากาศหรือเป็นรอยหยัก) นี้ก็คือ มันได้ทำให้เกิดแพทเทิร์นที่ดูแปลกตาออกไป ซึ่งตรงนี้อาจจะเป็นที่ถูกใจของตลาด niche หรือกลุ่มนักออกแบบที่มองหาความ unique มากๆ อย่างไรก็ดี เขาคงจะต้องกลับไปทำการบ้านซ้ำ และประเมินค่า “ความหนาแน่น” ที่เหมาะสมให้กับการม้วนแผ่นไม้นี้อีกครั้ง ทั้งนี้ก็เพื่อให้กระบวนการผลิตทั้งหมดเกิด “ความคุ้มค่า” อย่างสูงสุด และไม่ทำให้กระบวนการแปรรูปเชิงอุตสาหกรรมในขั้นต่อไปเกิดความ “ยุ่งยาก” เกินไปด้วย
ในเบื้องต้น นิพิฐพนธ์วางแผนว่าเขาอยากทำให้มวลวัสดุตั้งต้นนี้มีความคงทนแน่นหนามากขึ้น ซึ่งอาจจะใช้วิธีการเพิ่ม “สารเติมเต็ม” บางอย่างเข้าไปตามช่องโพรงต่างๆ ยกตัวอย่างเช่น อาจจะลองใช้ “เรซินใส” ยิงอัดเข้าไป และถ้ามันเป็นไปได้จริงดังคาด เขาก็จะลองเติมสีอื่นๆ หรือเศษวัสดุขนาดเล็กอื่นๆ (เช่น ขี้เลื่อย เศษฝุ่น ไฟเบอร์) ลงไปในตัวเรซินด้วย ทั้งนี้เพื่อจะให้มันเกิดสีสรรและ effect แปลกๆ ขึ้นในตัวมวลวัสดุ ก่อนที่จะนำมันไปผ่าเป็น section หรือไปแปรรูปใช้งานในเชิงอุตสาหกรรมต่อไป
นอกจากนั้นแล้ว อีกแนวทางหนึ่งที่นิพิฐพนธ์อยากเสนอให้ทางลีโอวูดนำไปพิจารณาด้วย ก็คือ การต่อยอดวัสดุตั้งต้นนี้ไปเป็น Architecture product ชิ้นสำเร็จบางอย่าง อาทิเช่น เป็นบานจับประตู ลูกบิดประตู โคมไฟ ขอบบัว ฯลฯ แต่ทั้งนี้เขาจำเป็นต้องอาศัยเวลาพลิกแพลงขั้นตอนการผลิตอีกเล็กน้อย รวมถึงต้องออกแบบเรื่องความหนาแน่นและการตัด section ให้กับตัววัสดุอีกครั้ง
ข้อเสนอแนะจากผู้เข้าร่วมเวิร์คชอป - วัสดุใหม่นี้มีความเป็นไปได้สูงที่จะพัฒนาต่อไปเป็นผลิตภัณฑ์ signature ของลีโอวูดได้ (เช่น เป็นบานจับประตู หรืออื่นๆ ที่กล่าวไปแล้วข้างต้น) ขึ้นอยู่กับว่าทางทีมงานจะหาชนิดของ “กาว” หรือ “ความบางของแผ่นไม้” ที่เหมาะสมได้หรือไม่ (เพื่อทำให้การม้วนและความหนาแน่นของมวลวัสดุเป็นไปอย่างที่ต้องการ) |
คู่ที่สี่: ผ้าผสมเส้นใยธรรมชาติ VS งานศิลปะเท็กซ์ไทล์ ผู้ผลิตวัสดุ: บัณฑิต พงศาโรจนวิทย์ (บริษัท ไทยนำโชคเท็กซ์ไทล์ จำกัด) ผู้ผลิตวัสดุผ้าผสมเส้นใยธรรมชาติ นักออกแบบ: ขนิษฐา นวลตรณี โจทย์ความเป็นไปได้ในการออกแบบ: นำวัสดุเส้นใยธรรมชาติไปประยุกต์ใช้ในแอพลิเคชั่นอื่นๆ |
ขนิษฐา นวลตรณี มีแนวคิดการสร้างลวดลายบนผืนผ้าให้ดูเป็นธรรมชาติมากที่สุด (ไม่เป็นบล็อกสี่เหลี่ยมที่เห็นแพทเทิร์นซ้ำๆ กันจนเกินไป) ที่สำคัญเธออยากจะให้ผลงานชิ้นนี้มีความสอดคล้องกับแนวคิดธุรกิจของไทยนำโชคที่ว่า “Nature is Future” ด้วย ในการนี้เธอได้นำทฤษฎี วาบิ ซาบิ (Wabi Sabi) หรือสุนทรียภาพตามธรรมชาติ มาสร้างเป็นกรอบแนวคิดในการออกแบบ (Design Criteria) โดยตั้งใจจะให้ชิ้นงานที่เกิดขึ้นสามารถเก็บงำความงามตามธรรมชาติของตัววัสดุที่ใช้ อาจมีผิวสัมผัสที่ไม่สม่ำเสมอตามลักษณะของเส้นด้าย มีสีสันที่เปลี่ยนแปลงไปตามกรรมวิธีย้อมสีธรรมชาติ รวมทั้งมีลวดลายการทอที่ดูไม่เป็นระเบียบ ไม่สมดุล แต่ยังแฝงความเรียบง่ายไว้ในภาพรวมทั้งหมด
ขนิษฐานำเสนอกระบวนการทำงานรอบนี้ใน 2 ส่วนหลักๆ คือ
1. แรงบันดาลใจ (Inspiration) เธอกล่าวว่าแรงบันดาลใจในการสร้างสรรค์ลายผ้าครั้งนี้เกิดจากการมองสภาพ “ประตูไม้เก่าแก่” ที่ผ่านร้อนผ่านฝนมากว่า 30 ปี โดยเธอได้นำเทคนิคการทอผ้าแบบมัดหมี่ซึ่งเป็นงานมือ (Handcraft) มาประยุกต์ใช้ แต่ก็ไม่ลืมที่จะคำนึงถึงความเป็นไปได้ในการผลิตแบบอุตสาหกรรมด้วย ในระหว่างการทำงานขนิษฐาเริ่มทดลองย้อมสีเส้นด้ายเพื่อใช้สำหรับการทอผ้า โดยเธอมีแนวคิดที่จะเปลี่ยนกระบวนการผลิตจากเดิมที่โรงงานมักย้อมสีผ้าแบบทั้งผืน มาสู่การย้อมสีบนเส้นด้าย (Yarn Dye) ก่อนจะนำไปทอเพื่อสร้างลวดลายต่อไป
2. การร่างแบบและขึ้นลาย (Experiment and Sketch) ขนิษฐาได้นำ “ลวดลายแห่งกาลเวลา” จากบานประตูไม้เก่ามาทดลองขึ้นลายบนคอมพิวเตอร์ (ก่อนจะนำไปผลิตจริงบนเครื่องทอของโรงงาน) ทั้งนี้เพื่อจะลดกระบวนการทำงานให้สั้นที่สุดตามกรอบเวลาที่มีจำกัด เธอกล่าวว่าการออกแบบโครงสร้างการทอนั้นสามารถสร้างลวดลายบนชิ้นผ้าได้เลยโดยไม่ต้องพิมพ์ลายทับซ้ำลงไปอีก ซึ่งสำหรับการทอผ้าแบบทั่วๆ ไปนั้นก็จะใช้งานเครื่องทอแค่ประมาณ 4-6 ตะกอ แต่สำหรับงานนี้เธอวางแผนที่จะใช้การทอแบบ 16 ตะกอ (ตามขีดความสามารถสูงสุดของเครื่องทอผ้า) เพราะอยากจะสร้างแพทเทิร์นให้ดูใกล้เคียงกับธรรมชาติมากที่สุด นอกจากนั้นขนิษฐายังได้กำหนดโครงสร้างของตะกอเป็นลักษณะเดียวแต่สามารถสร้างลวดลายบนชิ้นผ้าได้หลากหลาย (จากการยกตะกอที่ต่างกัน) รวมทั้งยังตั้งใจที่จะใช้เส้นด้ายหลายขนาดในการทอผ้าผืนเดียวเพื่อจะสร้างผิวสัมผัสให้คล้ายกับธรรมชาติมากที่สุดด้วย
ท้ายสุดขนิษฐาระบุว่าผลงานสิ่งทอครั้งนี้ของเธอจะมุ่งเป้าไปที่การใช้งานในกลุ่ม Home Furnishing หรือ Accessories เป็นหลัก อาทิเช่น หมอนอิง ผ้าบุเฟอร์นิเจอร์ กระเป๋า ฯลฯ เพราะตามคุณลักษณะตั้งต้นของเส้นใยแล้วน่าจะเหมาะสมกับการใช้งานในกลุ่มนี้มากที่สุด
ข้อเสนอแนะจากผู้เข้าร่วมเวิร์คชอป - คุณบัณฑิต (ผู้ผลิตวัสดุ) ชื่นชมแนวคิดการสร้างลวดลายบนผืนผ้าที่สามารถผลิตได้จริงในระบบอุตสาหกรรมขนาดใหญ่ |